Hay al menos tres factores que, en conjunto, han contribuido en los últimos años a aumentar la importancia del Condition Monitoring y el uso de tecnologías relacionadas con el de una maquinaria o planta industrial.
El primero de estos factores es, sin dudas, la llegada de la Industria 4.0 y, dentro de ella, la Smart Factory, o fábrica “inteligente”, que se basa en una arquitectura conectada, lograda principalmente gracias a la integración con numerosos dispositivos IoT.
El segundo está relacionado con el fuerte impulso hacia la digitalización, que contribuye a borrar la separación tradicional entre los mundos TI (Tecnologías de la Información) y OT (Tecnologías Operativas). Esto ocurre especialmente desde el punto de vista de las redes y sistemas, que históricamente eran prerrogativa de uno u otro ámbito.
El tercero, finalmente, tiene que ver con la búsqueda constante de optimización de los activos industriales, la mejora en el mantenimiento y la reducción de residuos. Todos estos objetivos se pueden alcanzar mediante el Condition Monitoring, gracias a su capacidad para controlar de manera continua y precisa los equipos que están en el sitio de producción.
¿Qué es el Condition Monitoring?
El Condition Monitoring, esencialmente, es el proceso de monitoreo continuo y en tiempo real de uno o más sistemas cuyo correcto funcionamiento se busca garantizar. Para ello, se suelen utilizar dos macrotecnologías: una instalada en la máquina y otra, generalmente conectada a una plataforma web.
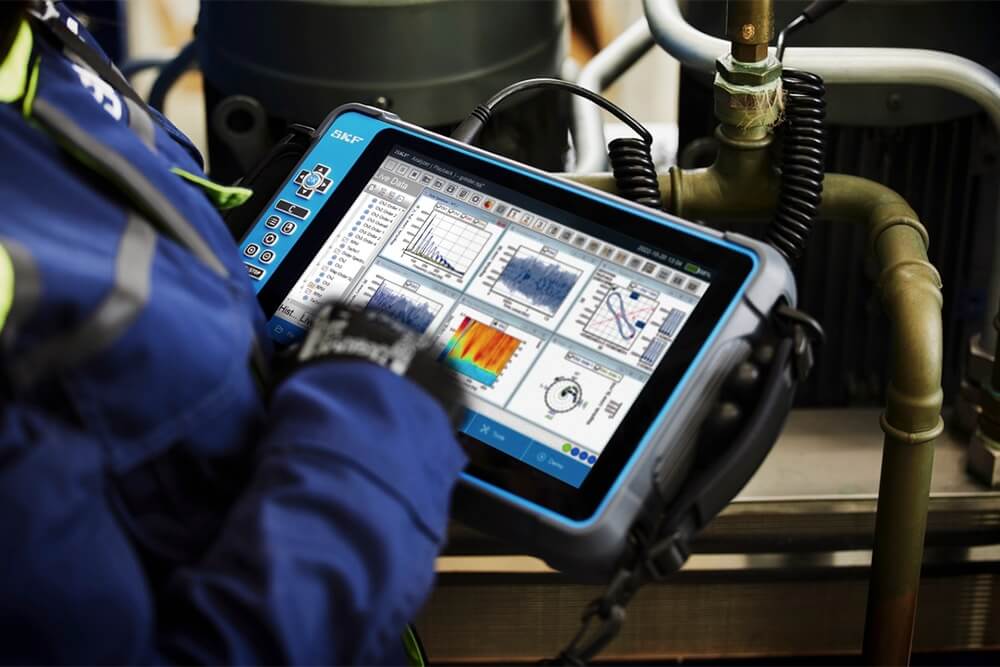
La primera consiste en sensores IoT, cada vez más integrados de manera nativa en las maquinarias, que tienen la tarea de capturar datos de funcionamiento. La segunda permite procesar esos datos en un entorno de nube o en el borde (edge computing) y devolverlos en forma de información útil sobre parámetros como la temperatura, las vibraciones, la presión, el estado de corrosión de las piezas mecánicas, el consumo promedio, entre otros.
Hasta hace poco, estas actividades requerían la inspección directa de un operador y, en muchos casos, un control que solo se podía realizar con la máquina detenida. El monitoreo de condición, en cambio, elimina tanto la necesidad de estar físicamente cerca del equipo como la de interrumpir los ciclos de producción para revisar los componentes menos visibles. Ahora, los paneles que presentan esta información, y que pueden consultarse desde una computadora o una tableta, muestran indicadores clave definidos por la empresa para evaluar la situación actual de cada sistema dentro de la planta.
¿Para qué sirve el Condition Monitoring?
Proteger plantas y activos industriales, extender su vida útil, planificar actividades de mantenimiento y reducir paradas inesperadas de producción son algunos de los beneficios que el Condition Monitoring puede garantizar.
No es casualidad que el mercado global relacionado con el hardware, software y servicios asociados al Condition Monitoring se haya estimado, en 2020, en 3092,2 millones de dólares. Este valor se proyecta a alcanzar los 5246,8 millones de dólares para 2026, con una tasa de crecimiento anual compuesta del 9,4%.
El motor principal de este crecimiento es la digitalización, que se vuelve cada vez más generalizada en sectores económicos como el petróleo y el gas, la automoción, la industria aeroespacial, la manufactura, la alimentación y las bebidas. En definitiva, cualquier sector que utilice equipos específicos en sus talleres, como correas, engranajes, cojinetes, motores, bombas hidráulicas, entre otros.
Además, hay una categoría de productos, agrupados bajo las siglas HVAC (Calefacción, Ventilación y Aire Acondicionado), que atraviesa todos los sectores y tiene una alta presencia. La monitorización precisa y constante de los sistemas HVAC tiene un doble propósito: garantizar su funcionamiento óptimo y, al mismo tiempo, verificar que su consumo energético cumpla con criterios de máxima eficiencia.
¿Cuáles son sus áreas de aplicación?
El uso de Condition Monitoring tiene aplicaciones en una amplia variedad de sectores. Además de su vínculo directo con la industria manufacturera, el monitoreo de sistemas se extiende a centrales hidroeléctricas y de energías renovables, la industria extractiva, el sector aeroespacial, el control de infraestructuras como puentes y viaductos, y también a la logística y el transporte.
Esta lista, aunque no exhaustiva, evidencia cómo en estos y muchos otros casos, la identificación de eventos inesperados que se desvían de lo normal se logra mediante algoritmos de aprendizaje automático. Estas tareas son difíciles de realizar con técnicas tradicionales de inspección y verificación del correcto funcionamiento de sistemas o equipos.
Este tipo de análisis, estrechamente ligado al Condition Monitoring, se conoce como detección de anomalías. Este proceso se basa en modelar algoritmos de aprendizaje automático al utilizar datos operativos históricos, con el objetivo de identificar posibles fallos antes de que se produzcan averías o incluso apagones en los sistemas analizados. Por este motivo, el Condition Monitoring encuentra en el mantenimiento predictivo su principal área de aplicación.
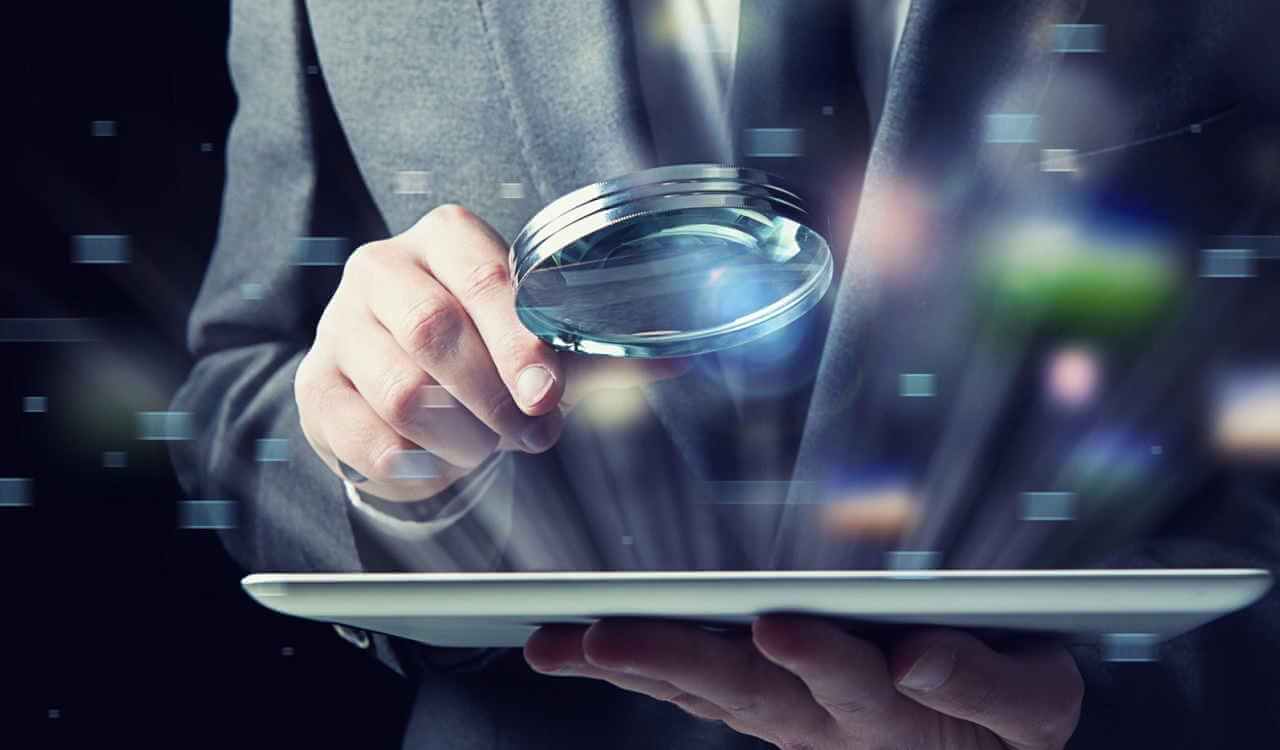
Condition Monitoring y mantenimiento predictivo y preventivo
El mantenimiento predictivo representa una evolución respecto al mantenimiento preventivo clásico. Este último consiste en una serie de intervenciones programadas, que suelen requerir paradas planificadas de las máquinas. Estas tareas, como calibración, limpieza y sustitución de componentes, se realizan en los intervalos recomendados por el fabricante y buscan extender la vida útil del sistema para que alcance la duración esperada.
Un ejemplo típico de mantenimiento preventivo fuera del ámbito industrial es el servicio periódico que realizás a tu auto. Sin embargo, el mantenimiento predictivo no es un reemplazo del preventivo, sino una integración que se apoya en datos obtenidos mediante herramientas y plataformas de Condition Monitoring. Este enfoque permite medir parámetros de forma continua y alertar al operador si alguno de ellos se desvía de las normas establecidas.
Las ventajas del mantenimiento predictivo son evidentes: desde la reducción de imprevistos y tiempos de inactividad hasta una mayor rapidez en las intervenciones y un ahorro significativo en los costos asociados a reparaciones posteriores al evento.
Por ejemplo, McKinsey reportó el caso de una empresa de petróleo y gas que implementó un avanzado sistema de mantenimiento predictivo en sus plataformas a partir de datos recopilados durante 30 años de operaciones. Los resultados fueron contundentes: una reducción promedio del 20% en el tiempo de inactividad y un aumento en la producción de más de 500.000 barriles de petróleo por año.